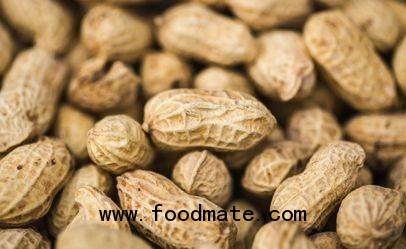
Inspectors from the U.S. Food and Drug Administration noted a string of unsanitary conditions at the company’s peanut butter processing plant between 2003 and 2011, reveal the newly published documents. Then, during its investigation following the Salmonella Bredeney outbreak this year, FDA discovered that the company had distributed peanut and almond butters that had tested positive for Salmonella a total of 21 times since 2009.
During the post-outbreak inspection, health officials found Salmonella in four samples of finished peanut butter product and one sample of shelled raw peanuts. Two of the strains found in the peanut butter are known to be Salmonella Bredeney. The serotypes of the other three were still being analyzed when the report was released.
Tests also revealed various stains of Salmonella in 23 samples swabbed from processing equipment and floors in the peanut butter plant. Three of these were S. Bredeney, nine were other strains, and the rest have yet to be analyzed, according to the report.
Inspectors noted an overall “failure to manufacture foods under conditions and controls necessary to minimize the potential for growth of microorganisms and contamination,” during their post-outbreak inspection – conducted between September 17 and October 16, 2012.
A total of nine other violations were also recorded. Among the problems that lead to these citations were:
- Equipment on processing and packaging lines was not properly cleaned
- Surfaces where dry product is processed were damp
- The construction of some processing equipment doesn’t allow for proper cleaning
- Some food contact surfaces were uneven, a condition that allows for the harboring of pathogens
- Employees were observed not washing hands before handling product, and adequate hand washing facilities were not provided.
- In-shell peanuts were stored outside in open containers where they were vulnerable to contamination
- Product was not adequately protected from pests. In one instance, bird feces was observed on a pallet of almond butter containers.
A History of Sanitation Issues
A look back at inspection reports from previous years shows that this was not the first time Sunland’s peanut butter plant was found to be operating under unsanitary conditions. In fact, it was the fifth time in six years.
In 2007, inspectors found that employees were not washing hands or sanitizing equipment properly, nor were adequate hand washing stations available. Holes were found in both the wall and manufacturing equipment and products were stored in containers that did not protect them from pests. A total of six violations were cited in FDA’s 483 report, issued to the company post-inspection.
FDA also found Salmonella in a sample swabbed from the door leading into the grinder room. The 60 other samples taken from the facility tested negative.
In this 2007 report, FDA mentions a previous 2003 inspection during which five violations were noted. Two of these had not been corrected by the time of the 2007 inspection, according to the document. These included inadequate pest control and parts of the building in disrepair.
By the next time FDA visited the plant, in 2009, only two of the six violations noted in 2007 had been corrected. Continuing problems included a failure to minimize the risk of microbial growth, a failure to minimize the risk of contamination, improper employee hand washing and a failure to adequately protect against pests.
An environmental sample taken during this 2009 inspection tested positive for Salmonella.
The following year, another inspection revealed that the company was still not taking adequate precautions against contamination or pests. The other previous problems appear to have been fixed; however floors were found to be in disrepair, male employees were not using proper beard protection and equipment was not found to be constructed to prevent product adulteration.
Finally, in March of 2011, FDA conducted its last inspection of the plant before this year’s outbreak – which began in June and lasted through September. During that visit, inspectors found two violations at company facilities: 1) Raw in-shell peanuts were being stored in a way that didn’t protect against contamination, and 2) Adequate pest prevention measures were still not in place.
Sunland reported in a letter dated April 13, 2011, that it had taken measures to correct both problems. The company responded to FDA with similar letters of correction after its 2009 and 2010 inspections.
History, Repeated?
The results of this investigation are eerily similar to what was discovered about the Peanut Corporation of America in the wake of the devastating 2008-2009 Salmonella outbreak linked to peanut products from that company.
Just as Sunland shipped product after samples tested positive for Salmonella, executives at PCA allegedly ordered peanuts to be shipped to processors after internal testing had detected Salmonella in samples of the nuts.
At least 700 people were sickened in that outbreak, and 9 died as a result of their infections.
Victims of the PCA outbreak and their families have called on the government to press criminal charges against Stewart Parnell, the company’s former CEO, who reportedly sent an email to his plant manager regarding the contaminated peanuts, ordering him to “turn them loose.”
Sunland’s Portales, New Mexico peanut and peanut butter plants were shut down after health officials linked the company to the Salmonella Bredeney outbreak in September. To date, the company has yet to resume operations.