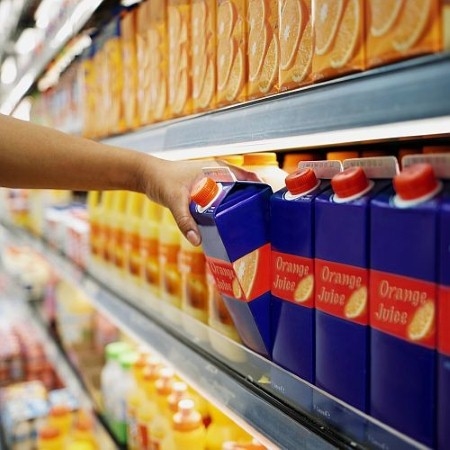
Thankfully, the advancement in materials for pre-packaged and take-out foods has made it possible to bring home pizza without the greasy mess. Consumers want a container that will keep food safe from outside contaminants, and one that is also strong and durable.
In addition to performance demands, there are other factors that influence shoppers’ decisions. The desire for a more retro, greener and nostalgic feel is allowing paperboard packaging to make a comeback. The design stands out amongst shelves full of glossy stand up pouches and rigid containers, catching consumers’ attention. While supply chain members and consumers alike continue to revel in the trend, compromising performance is not an option.
To address a growing demand for high-performing materials for this particular application, Dow Performance Packaging patented the BLUEWAVE™ Process Technology. The process takes molten polyolefins and disperses them in water, giving manufacturers the opportunity to create coating materials out of ubiquitous, non-self-dispersing polyolefins or plastomers. A winning combination was created when Dow acquired Rohm and Haas in 2009. Bringing together Dow’s polyolefin expertise and Rohm and Haas’ emulsion knowledge resulted in the development of a very robust technology that has led to dramatic acceleration of next-generation product development.
HYPOD™ Water-Based Polyolefin (PO) Dispersions was one such novel product, a portfolio of coating materials that continue to build on the impact made in the packaging industry by offering cost-saving, performance and sustainability benefits. Developed in 2005 and used in its first application in 2008, the water-based PO dispersion relieves manufacturers from having to make a choice. In packaging applications, the product enables heat seal coating at a very low initiation temperature for applications including pet food bags, pizza boxes, sandwich wrappers and candy.
In the past, manufacturers were unable to take advantage of PO performance benefits in a water-based system. They were stuck choosing between traditional ester acrylics, styrene butadiene rubber (SBR) latex or vinyl acetate emulsions for their coating needs. Now, the unique dispersion technology serves as another revolutionary option.
Over the past several years, Dow worked closely with customers to tailor the multifunctional coating technology to meet specific demands, to create versatile solutions. While traditional dispersions offer only a few advantages, HYPOD dispersions delivers a multitude of performance, design and manufacturing benefits including:
• Good oil and grease resistance
• High molecular weight and solids content, with 40 to 55 percent solids
• pH levels ranging from 8.5 to 10.5
• Heat sealability to polar substrates such as metallic or foil, and non-polar substrates like polyethylene (PE) and paper
• Generally compliant with European Union (EU) regulation 10/2011 with some SML limits, and the U.S. Food & Drug Administration (FDA) food contact regulations
• Excellent water resistance and moisture barrier for leak-free, water-proof packaging applications
• Low viscosity for packaging design flexibility
• Extends the use of polypropylene (OPP) films in high speed packaging applications
• Improved control compared to incumbent materials during coating in either the spray or foam format
In addition to its performance benefits, the water-based dispersion is also sustainable. According to Dow’s Sustainability Footprint Tool© the solution provides potential sustainability advantages compared to incumbents. The tool, which considers six sustainability dimensions with life cycle thinking, shows that HYPOD dispersions take sustainability to the next level. The technology requires fewer binders than conventional applications; maintains a faster, more efficient drying time; is recyclable in mainstream municipal channels; and delivers the opportunity for less water and energy consumption. For example, current low temperature sealing coatings (LTSC) seal at an initiation temperature of 70 degrees Celsius, whereas HYPOD dispersions seal at 60 degrees Celsius, broadening the heat seal processing window.
The water-based polyolefin dispersions also help create a safer environment for workers. The technology eliminates organic and volatile organic solvent emissions when compared to existing solvent-based coatings, making it enormously beneficial to converters trying to meet their emissions goals and increase workplace safety.
Another influential factor for new package development is cost. As a drop-in that is easy to use, the water-based solution can be quickly incorporated into existing production lines, and doesn’t require new machines or additional employee training. It provides lower production costs through thinner coatings on industrial horizontal form fill and seal (HFFS) lines and vertical form fill and seal (VFFS) lines, and can deliver lower energy costs through its higher solids content with lower drying times.
While cost remains a top priority for supply chain members and brand owners, the solution does not withhold on performance at low coating weights. Customers can add additional functionalities tailored to their packaging needs, like upgrading their current paperboard package to one that has a softer touch and superior wet strength. This water-based dispersion offers customers a toolbox of options that boost a wide range of attributes including:
• Sealability
• Moisture protection
• Haptics modifications
From performance benefits, to stringent food contact requirements and the patented BLUEWAVE Process Technology, the HYPOD dispersions portfolio is another example of how chemical companies can play a vital role in the supply chain and can be a resource for creating new packaging solutions.