Millions of tons of Polypropylene film are used to wrap billions of flow wrapped products every year. In many instances a carrying tray or punnet is also required to transport product through a flow wrapping machine. If even a fraction of a gram of packaging material in each package can be saved the overall effect provides sizable benefits for the environment as well as giving lower packaging costs which in turn means higher profit margins for the manufacturer. A packaging trend can be seen in the move towards flow wrapping product without a carrying tray or punnet bringing immediate savings in both packaging material and packaging costs. However the challenge for Redpack is to ensure that product being wrapped without a tray is not damaged or bruised as it progresses through the Flowrapper.
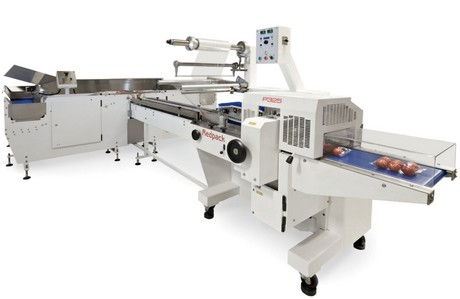
Redpack’s latest machine design is leaving a rosy impression on apple growers and packers. Apple growers have been demanding a flow wrapping machine that can wrap apples without a tray and in a format to suit supermarket shelves. However apples are notoriously easy to damage and bruise so have to be handled very carefully “soft packaging” as it’s known in the trade. Redpacks P325S with “Frictionless Infeed” (P325S-FI) has been developed to provide damage free transportation of fruit along the infeed and transfer onto the wrapping film.
As a further improvement Redpack have configured the product infeed so that apples can be collated in “Soldier Packs” of 4, 6, 8 or 10 without the need for infeed change parts. Pitch variation is carried out by a simple handwheel adjustment and with wrapping speeds of around 60ppm the Growers and Packers will be doubling the packing speed compared to their old packaging method. According to Redpacks Marketing Manager:
“Apple Packers are very excited about the new P325S frictionless infeed flow wrapper because it doesn’t damage the fruit, can be easily adjusted for different size packs, doubles their packaging speed and saves them money on their packaging materials. You could say that it’s a real windfall for them”
Of course it’s not just apples that can be wrapped on the P325-FI other fruit of similar size, pears, oranges, lemons, etc. will benefit from this new machine configuration.
Redpack Packaging Machinery is leading the way in “Trayless” flow wrapping development. Over the last 16 months 60% of Redpacks machine production has been for wrapping product without trays and they have built an impressive portfolio of machine configurations. For example Redpacks HTS flow wrapping machine has an inverted seam crimp and reel handling mechanism, an arrangement generally referred to as a Top Seal or Inverted flow wrapping machine, it is most effective for a very wide range of Fresh Produce and delicate or difficult to transport products.
Further film savings are achieved on the HTS flowrapper by designing the product infeed so that it will only flow when product is in place, if no product is detected the wrapping module stops preventing empty bags from being produced. This feature can be combined with product detection that causes the machine to alter the bag length to suit the length of the product, leeks for instance can have significant length variation but with a “cut to length” arrangement the bag length is always just long enough. Both “no product no bag” and “cut to length” features achieve significant savings in film wastage.
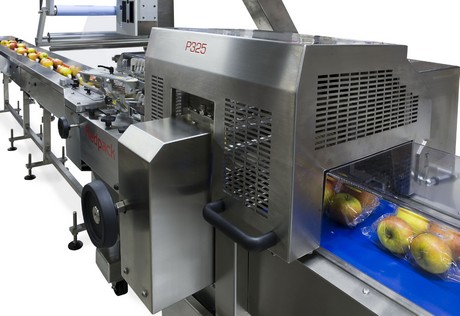
Redpack design and manufacture trayless machines that have automatic feed systems for example for trayless tomatoes a P325 flow wrapper is married to an automatic tomato feeder to gently feed the tomatoes to the flowrapper infeed, packaging speeds in excess of 110ppm can be expected.
Redpack Packaging Machinery are eager to work with growers and packers to develop trayless packaging and to help them to make a positive contribution to their companies profitability and towards a cleaner environment by making savings in packaging material usage. In addition it is likely that there will be improvements in packaging speeds and machine versatility that will lead to fast payback on flow wrapping machine investment.