PDXTM Reactor
Dramatically reduces cooking/processing time whilst at the same time improving quality. The PDXTM reactor homogenises, mixes, heats and pumps simultaneously with unequalled performance. The results are quite staggering:
• Larco Foods are already benefiting from a 78% reduction in production time for 700kg of béchamel sauce to 6 minutes.
• Energy consumption is reduced by up to 40%
• Health benefits are generated from the improved mixing process that allows certain ingredients such as salt to be reduced.
With the UK government pushing to reduce salt intake to 6g a day by 2015 and 3g by 2025, the PDX reactor is the technology to facilitate this.
PDX™ 3D Scan
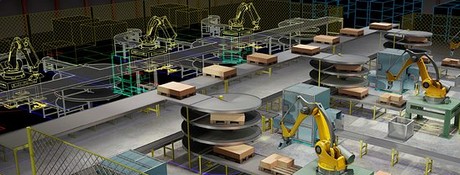
Your whole factory, accurate to 2mm, measurable at your desk. The PDX™ 3D Scan provides revolutionary 3D factory walk-throughs, reduces the time to create 3D factory layouts by a factor of twelve, and removes manual measurements giving pin-point accuracy. With the PDX™ 3D Scan share best practices across sites and remodel whole areas faster.
Virtually all of the food industry is facing increasing pressure from retailers to guarantee that packaging and date codes are correct to prevent product recalls. If mistakes happen involving the wrong packaging or worse, the wrong date code, the food processor can expect a fine of over £50,000 and product returns. Get it wrong more than once and the processor risks losing the business.
How can Olympus Automation eliminate that risk?
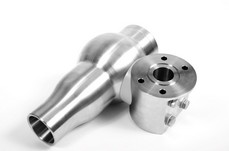
The PDX™ End of Line system removes the risk of product recalls, takes away much of the paperwork and provides an accurate, real-time, measurement of production performance in a single solution. Deployment starts with the installation of a touch screen on each line to give feedback to the operator and provide direct links to key equipment and drive other devices like bar codes scanners.
Once the hardware is in place the date code process is made ‘mistake proof’ by removing the need for the operator to enter date codes. Direct control of the printer from authorised product standards means changeovers and special offers are all covered automatically.
The system uses unique 2D barcodes, accepted by all the major retailers, printed onto all film and packaging. To maintain total security these include: packs, film, pots, lids; everything that makes up the finished product. All that’s left is for the operator to make sure they select the right product; if they get that wrong the 2D bar code scans will pick up the error and stop the line.
To further increase security paperless QA checks can be established to ensure the operator performs key checks at set times. These include product images via the colour bar code scanner to confirm products run and improve product traceability.
“From a technical point of view, Olympus Automation understood not only our needs but our customers’ need as well. The system is easy to use and gives you peace of mind and reassurance that the correct dates and packaging are on the product.” Eleanor Agnew, Technical Manager, Blue Earth Foods.
Combine Security with Performance
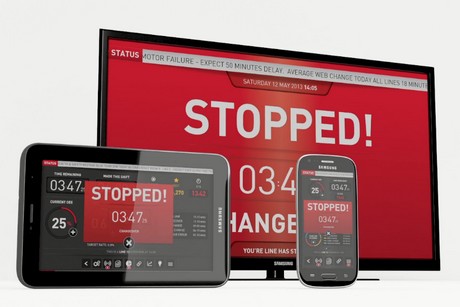
PDXTM Performance is an innovative software that ‘bolts onto' End of Line capturing and reporting downtime in real-time, on the same hardware. The single system operates across smartphones, tablets, touch screens, desktops and large shop-floor displays and is designed to filter distractions and provide the operations team with the information they need.
Mobile Reporting and Intelligent Targeting
Individuals have different reporting needs; whilst operators are usually close to a line, team leaders have a roving brief so real-time information has to be mobile with targeted information tailored to their needs.
PDX™ Performance delivers accurate, real-time information where your team needs it, on the shop-floor pushing hard for improvements, not tied to an office desktop generating yesterday’s reports.
“We chose the Olympus Automation packaging and date control solution as reference visits proved their system to be reliable. Their variety of add-on modules meant we were able to include performance reporting and live checkweigher links to meet the growing demands of our business,” explains Jarnail Sani, Director of Operations, Adams Foods.