The Ishida Seal Tester is able to test the integrity of sealed, flow-wrapped or lidded trays in a wide variety of materials and sizes. The system applies controlled pressure to each tray going across a conveyor and detects and evaluates any subsequent ‘give’. Advanced servomotor control minimises vibration of the testing plate and ensures that contact with the pack is optimal, allowing maximum dwell time for greater leak detection accuracy.
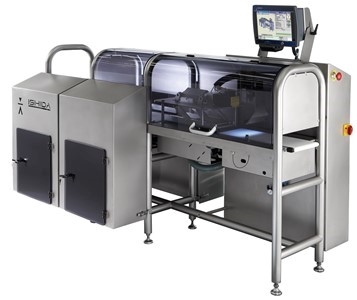
A major benefit of the process is that the testing process is non-destructive, meaning failed pack contents can be re-packed. In addition, as well as detecting significant leakages, the system can pick up any trends that give an early warning of deterioration in the sealing process, either from the tray sealer itself or the tray thermoformer.
The Seal Tester can operate on both a continuous and intermittent basis, detecting a 1mm hole at speeds of up to 140 packs per minute. It can also be used to establish the maximum ‘safe’ pressure that can be applied to a given pack. A choice of two or four reject bins is available.
The Ishida Vision System verifies the accuracy of the tray label, ensuring that it is positioned correctly and relating the overprinted data to the company’s information systems to check that dates, weights, prices and barcodes (including 2D versions) are correct and legible. Images and results of these quality checks can be archived for evidence in the event of any subsequent problem or complaint.
“Tray leaks can be a major cause of contamination and returns from retailers, and this is making the need for both effective detection and traceability of out-of-spec packs increasingly important throughout all sectors of the fresh food industry,” comments Torsten Giese, Marketing Manager - PR & Exhibitions of Ishida Europe. “Failure to do this can lead to product returns, retailer fines and the loss of brand reputation.
“The new Ishida Seal Tester and Vision System combination provides a comprehensive fast and reliable quality check. Equally important, it enables companies to continue the automated process into the packing of trays into cartons or crates, delivering efficiencies and cost savings in the reduction of manual labour.”