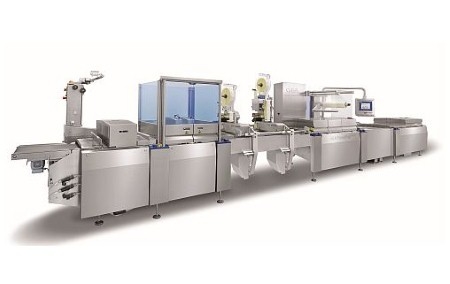
The output of thermoformers plays a crucial role when fresh food is being packed. The rate of production must keep pace with constantly escalating requirements if food producers are to remain competitive.
Outlined below is a comparison of two concepts, each of which promises to deliver greater efficiency during the packaging operation. The option ultimately selected by the company in question depends on several factors, including the production environment.
There are two fundamental approaches to increasing output or performance: first, processing more packs per cycle, and second, running more cycles per minute. "There is no silver bullet," says Stefan Krakow, head of thermoformer product management at GEA Food Solutions GmbH, who recently gave a presentation on the subject of efficiency enhancement with thermoforming machines at the company's headquarters in Biedenkopf. "Each option has specific pros and cons. First of all, a decision has to be taken on the most suitable packaging concept for the relevant production environment.“ GEA Food Solutions offers appropriate machine configurations for both approaches.
Urging caution, Krakow continues, "One thing is certain, however: if the upstream and downstream processes are unable to match the increased packaging output, the outcome is fruitless. If the individual influencing factors are not examined in unison, the decision in favour of a new machine concept will be made ineffective by the peripheral conditions." When seeking to pack sausage, cheese, meat or other fresh produce with an elevated cycle speed, consideration must be given to an abundance of criteria in order to achieve a sound outcome. Only then can process reliability and overall quality, as well as high product yield and portion quality be guaranteed in the long run.
Factors influencing the packaging process
In food packaging, a lot of attention must be paid to external factors. These include packaging material behaviour, which has a direct impact on the heating, forming and sealing processes. In this connection, close collaboration with the film producer is crucial. Among the other vital aspects are the product properties and the upstream and downstream operations in the packaging process, namely slicing, conveying, loading, converging, inspection, labelling, aggregating and group packaging, each of which must be able to handle the increased output. Another external factor is the supply of compressed air, low pressure for a vacuum, electricity and water. "Especially as regards the vacuum," explains Krakow, "the prevailing conditions often oppose the goal of increased performance."
A whole raft of machine-specific factors, in particular process times, likewise exert an influence on packaging output. Process times are determined by the signal processing speed and the generation and holding of pressures and temperatures. Krakow comments, "Only stable systems that avoid major fluctuations can give rise to enhanced performance." In this context, pack evacuation and gassing are also significant issues.
When designing a thermoforming packaging machine, one of the goals is to achieve universality. When seeking to
increase output by raising cycle speed, however, this target is difficult to meet. Efficiency and speed in packaging cannot be accomplished without defining specific design parameters. In this connection, kinematics, motion times, die volumes and weights, pressures and pressure differences are key considerations both in valve design and during the packaging operation.
Focus on process times
This wide variety of influences raises the question as to where exactly to leverage performance increases with thermoforming machines, especially since the underlying machine concept has already been refined over many years. Can the machine control or individual components be designed more intelligently in order to raise the packaging speed substantially?
Some design scope has been identified for significantly accelerating the overall process by modifying the sealing operation and process times – in particular for product evacuation.
Concept 1: More packs per cycle
The PowerPakNT is a modular thermoformer that satisfies the most demanding packaging aspirations and output requirements. Its high performance is underpinned by very generous index lengths and relatively wide webs, which combine to provide the surface area required for processing a large number of packs per machine cycle. In the case of a typical presentation pack for a sliced and shingled product with a 4x6 format – 24 packs per cycle, for example, an index length of approx. 1.2 m and a film width of approx. 700 mm can be used. Operating at a rate of approx. 10 cycles/min, the machine thus achieves an output of approx. 240 packs/min. With squarer packs and therefore higher utilisation of the available area, performance can edge above 300 packs/min.
The aggregate die length can reach up to approx. 2.5 m. The forming frame weighs around 280 kg, and the deep-draw lid approximately 450 kg. With this model, the total weight of the format parts is around 1.8 metric tons. "When the dies are being changed, a lot of weight has to be shifted," says Krakow, "which calls for appropriate tools, an adequate time allowance and great care."
These are special-purpose, expensive machines, so that procuring specific spare parts can be difficult. The PowerPakNT also occupies a relatively large area; it is fairly long and the die components are quite heavy. In view of the special film widths, moreover, the number of material suppliers is inevitably restricted. Each of these elements has an impact on the overall cost structure. "The PowerPakNT is nonetheless established on the market," remarks Krakow. "It can be tailored to meet specific needs by way of customisable modules, extended at any time, and ranks among the very best as regards output."
Concept 2: More cycles per minute
The PowerPakSpeed, in turn, is a high-speed thermoformer designed specifically for two applications, namely shingled products in typical self-service portions, and hot dogs packaged in one or two layers in flat MAP trays or vacuum packs.
The key benefits afforded by this machine type include its conventional dimensions, and die components with standard dimensions and weights, so that ease of operation is ensured. The 560 mm film width allows the use of standard films, which are available from a large number of suppliers. When processing typical self-service packs, the PowerPakSpeed achieves an output of 200 to 240 packs/minute.
In view of its narrower application scope, the PowerPakSpeed can dispense with the large variety of functions offered by a standard general-purpose thermoformer. As a general rule, the specifications of universal systems entail compromises to the detriment of productivity. In order to achieve a higher speed in this case, improved technologies were developed for the most time-consuming operations. Depending on the operating environment, the PowerPakSpeed can be as much as 50 percent faster than standard machines. "This packaging machine is designed for speed when processing compatible sliced and shingled products. However, the upstream and downstream operations must be able to keep pace with the high output," insists Krakow.
From evacuation to sealing
Measured against a typical standard machine, the PowerPakSpeed reduces the evacuation time from approx. 1.3 s to around 0.5 s. "In other words, half the battle is already done when seeking to accelerate the packaging speed," claims the product manager. The time saving is achieved by way of a stable vacuum and adequate dimensioning; the goal is to provide a central vacuum with a constant, maximum reserve of 4 mbar, depending on the necessary residual oxygen values. When the air is evacuated from the pack in the machine's sealing station, the pressure is suddenly equalised in a pre-evacuated space. Other design modifications have been made concerning the valve arrangement and hoses, which also have an impact on the process.
A further substantial time saving is made for the benefit of the entire process in the sealing operation. A short sealing time is key – with the PowerPakSpeed it is less than 0.5 s. "It cannot be achieved with all materials; it is essential to engage in an intensive dialogue with the film supplier during the implementation phase. The packaging material must be compatible with fast sealing," explains Krakow. "Suitable materials are already available from a large number of prospective suppliers."
The design engineers also focused on servo technology for all the travel and die cutting movements, so that both models offer fast cycle times and perfectly attuned, energy-efficient movements.
Smooth interaction
The declared development goal was to reduce the overall cycle time of the PowerPakSpeed by approx. two seconds in order to accomplish the desired change in the number of cycles per minute. The cycle rate of a standard machine stands at around 10 to 13 cycles/min. The PowerPakSpeed, in contrast, delivers a performance of approx. 22 to 24 cycles/min. Krakow concludes, "If the product and logistics are well matched, a packaging concept that envisages more cycles per minute is ultimately more productive in many cases than one that processes more packs per cycle."
The business benefits for the user are self-evident. The workflows of many companies are built on readily manageable components and, in view of the relatively small footprint, our machines can easily be integrated in existing lines. "In combination with our high-performance slicing, loading, converging, printing and labelling systems, moreover, we can place at the customer's disposal a forward-looking concept that ensures both smooth interaction and high availability long-term."
Outlined below is a comparison of two concepts, each of which promises to deliver greater efficiency during the packaging operation. The option ultimately selected by the company in question depends on several factors, including the production environment.
There are two fundamental approaches to increasing output or performance: first, processing more packs per cycle, and second, running more cycles per minute. "There is no silver bullet," says Stefan Krakow, head of thermoformer product management at GEA Food Solutions GmbH, who recently gave a presentation on the subject of efficiency enhancement with thermoforming machines at the company's headquarters in Biedenkopf. "Each option has specific pros and cons. First of all, a decision has to be taken on the most suitable packaging concept for the relevant production environment.“ GEA Food Solutions offers appropriate machine configurations for both approaches.
Urging caution, Krakow continues, "One thing is certain, however: if the upstream and downstream processes are unable to match the increased packaging output, the outcome is fruitless. If the individual influencing factors are not examined in unison, the decision in favour of a new machine concept will be made ineffective by the peripheral conditions." When seeking to pack sausage, cheese, meat or other fresh produce with an elevated cycle speed, consideration must be given to an abundance of criteria in order to achieve a sound outcome. Only then can process reliability and overall quality, as well as high product yield and portion quality be guaranteed in the long run.
Factors influencing the packaging process
In food packaging, a lot of attention must be paid to external factors. These include packaging material behaviour, which has a direct impact on the heating, forming and sealing processes. In this connection, close collaboration with the film producer is crucial. Among the other vital aspects are the product properties and the upstream and downstream operations in the packaging process, namely slicing, conveying, loading, converging, inspection, labelling, aggregating and group packaging, each of which must be able to handle the increased output. Another external factor is the supply of compressed air, low pressure for a vacuum, electricity and water. "Especially as regards the vacuum," explains Krakow, "the prevailing conditions often oppose the goal of increased performance."
A whole raft of machine-specific factors, in particular process times, likewise exert an influence on packaging output. Process times are determined by the signal processing speed and the generation and holding of pressures and temperatures. Krakow comments, "Only stable systems that avoid major fluctuations can give rise to enhanced performance." In this context, pack evacuation and gassing are also significant issues.
When designing a thermoforming packaging machine, one of the goals is to achieve universality. When seeking to
increase output by raising cycle speed, however, this target is difficult to meet. Efficiency and speed in packaging cannot be accomplished without defining specific design parameters. In this connection, kinematics, motion times, die volumes and weights, pressures and pressure differences are key considerations both in valve design and during the packaging operation.
Focus on process times
This wide variety of influences raises the question as to where exactly to leverage performance increases with thermoforming machines, especially since the underlying machine concept has already been refined over many years. Can the machine control or individual components be designed more intelligently in order to raise the packaging speed substantially?
Some design scope has been identified for significantly accelerating the overall process by modifying the sealing operation and process times – in particular for product evacuation.
Concept 1: More packs per cycle
The PowerPakNT is a modular thermoformer that satisfies the most demanding packaging aspirations and output requirements. Its high performance is underpinned by very generous index lengths and relatively wide webs, which combine to provide the surface area required for processing a large number of packs per machine cycle. In the case of a typical presentation pack for a sliced and shingled product with a 4x6 format – 24 packs per cycle, for example, an index length of approx. 1.2 m and a film width of approx. 700 mm can be used. Operating at a rate of approx. 10 cycles/min, the machine thus achieves an output of approx. 240 packs/min. With squarer packs and therefore higher utilisation of the available area, performance can edge above 300 packs/min.
The aggregate die length can reach up to approx. 2.5 m. The forming frame weighs around 280 kg, and the deep-draw lid approximately 450 kg. With this model, the total weight of the format parts is around 1.8 metric tons. "When the dies are being changed, a lot of weight has to be shifted," says Krakow, "which calls for appropriate tools, an adequate time allowance and great care."
These are special-purpose, expensive machines, so that procuring specific spare parts can be difficult. The PowerPakNT also occupies a relatively large area; it is fairly long and the die components are quite heavy. In view of the special film widths, moreover, the number of material suppliers is inevitably restricted. Each of these elements has an impact on the overall cost structure. "The PowerPakNT is nonetheless established on the market," remarks Krakow. "It can be tailored to meet specific needs by way of customisable modules, extended at any time, and ranks among the very best as regards output."
Concept 2: More cycles per minute
The PowerPakSpeed, in turn, is a high-speed thermoformer designed specifically for two applications, namely shingled products in typical self-service portions, and hot dogs packaged in one or two layers in flat MAP trays or vacuum packs.
The key benefits afforded by this machine type include its conventional dimensions, and die components with standard dimensions and weights, so that ease of operation is ensured. The 560 mm film width allows the use of standard films, which are available from a large number of suppliers. When processing typical self-service packs, the PowerPakSpeed achieves an output of 200 to 240 packs/minute.
In view of its narrower application scope, the PowerPakSpeed can dispense with the large variety of functions offered by a standard general-purpose thermoformer. As a general rule, the specifications of universal systems entail compromises to the detriment of productivity. In order to achieve a higher speed in this case, improved technologies were developed for the most time-consuming operations. Depending on the operating environment, the PowerPakSpeed can be as much as 50 percent faster than standard machines. "This packaging machine is designed for speed when processing compatible sliced and shingled products. However, the upstream and downstream operations must be able to keep pace with the high output," insists Krakow.
From evacuation to sealing
Measured against a typical standard machine, the PowerPakSpeed reduces the evacuation time from approx. 1.3 s to around 0.5 s. "In other words, half the battle is already done when seeking to accelerate the packaging speed," claims the product manager. The time saving is achieved by way of a stable vacuum and adequate dimensioning; the goal is to provide a central vacuum with a constant, maximum reserve of 4 mbar, depending on the necessary residual oxygen values. When the air is evacuated from the pack in the machine's sealing station, the pressure is suddenly equalised in a pre-evacuated space. Other design modifications have been made concerning the valve arrangement and hoses, which also have an impact on the process.
A further substantial time saving is made for the benefit of the entire process in the sealing operation. A short sealing time is key – with the PowerPakSpeed it is less than 0.5 s. "It cannot be achieved with all materials; it is essential to engage in an intensive dialogue with the film supplier during the implementation phase. The packaging material must be compatible with fast sealing," explains Krakow. "Suitable materials are already available from a large number of prospective suppliers."
The design engineers also focused on servo technology for all the travel and die cutting movements, so that both models offer fast cycle times and perfectly attuned, energy-efficient movements.
Smooth interaction
The declared development goal was to reduce the overall cycle time of the PowerPakSpeed by approx. two seconds in order to accomplish the desired change in the number of cycles per minute. The cycle rate of a standard machine stands at around 10 to 13 cycles/min. The PowerPakSpeed, in contrast, delivers a performance of approx. 22 to 24 cycles/min. Krakow concludes, "If the product and logistics are well matched, a packaging concept that envisages more cycles per minute is ultimately more productive in many cases than one that processes more packs per cycle."
The business benefits for the user are self-evident. The workflows of many companies are built on readily manageable components and, in view of the relatively small footprint, our machines can easily be integrated in existing lines. "In combination with our high-performance slicing, loading, converging, printing and labelling systems, moreover, we can place at the customer's disposal a forward-looking concept that ensures both smooth interaction and high availability long-term."