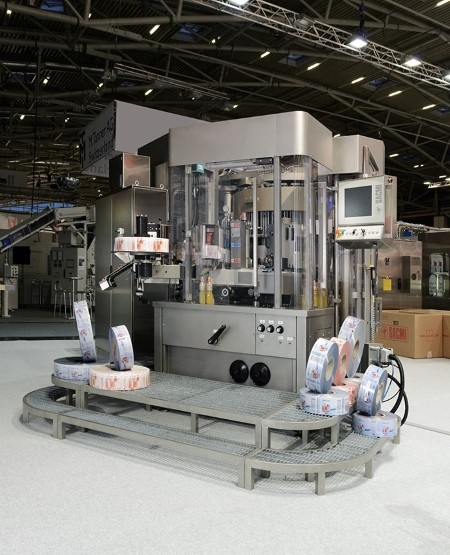
The displayed machines will include the 32-cavity CCM, a compression press for the manufacture of plastic caps, characterised - just like the rest of the CCM range - by the low temperatures at which the extrusion process takes place, thus ensuring considerable advantages on the energy-saving and productivity fronts. Equipped with an innovative 'COOL+' mould designed to enhance the efficiency of the cooling process even further, at the fair the CCM32 will be making soft drink closures with cycle times of approximately 2 seconds, a speed that makes this the most competitive cap production solution in the world. A Sacmi-made 2-camera Sacmi CVS3000 Quality Control system integrated on the CCM ensures 100% guaranteed cap quality.
A global pioneer that is revolutionising closure products and processes (at present, 40% of the world beverage market uses Made-in-Sacmi compression technology), Sacmi will also be making the very most of the opportunities presented by Europe's biggest packaging fair to showcase COLORA CAP, the new on-cap digital printing system that allows high-definition images to be printed directly on the production line without having to store the caps; the user can also effect real-time decoration changeovers simply by switching to a different graphics file: a major competitive advantage for manufacturers, then, in terms of both output flexibility - the machine can carry out any type of on-cap decoration (e.g. promo campaigns, events, prizes etc.) - and stock management, allowing HD images to be printed on caps in just a few minutes, even on small production runs. The Sacmi CVS3000 Quality Control system, stationed both upstream and downstream from COLORA CAP, ensures that only flawless caps are decorated and only those with fault-free images are used in bottling.
Moving on to labelling: Sacmi will also be heading to Düsseldorf with the latest plant engineering solutions from Sacmi Verona. Following an extensive overhaul in 2013, the Sacmi labelling range now includes the flagship FORMSLEEVE+, the new modular labeller offering outstanding output versatility and unique levels of flexibility in the choice and control of materials. The machine is designed, in fact, to form the sleeve directly in the machine from the roll using natural bonding liquids, cutting label costs by over 20%. Product quality is guaranteed by the LVS360 which, thanks to innovative software, unrolls the 3-D image provided by the 4 cameras to form a 2-D image that allows inspection of 100% of the label.
On the quality control front, Sacmi will be presenting the PVS and CHS vision systems at the fair. Designed for direct installation on the line, next to the press, the PVS system can test an impressive quantity of preforms - up to 36,000 an hour - at set time intervals, either feeding them back into the production cycle or, should they fail to respond to set quality parameters, tripping an alarm: an efficient solution that eliminates potential defects and, thanks to high levels of system automation and reliability, minimises line downtimes. Alongside the PVS, Sacmi also offers the new CHS cap control system: equipped with HD video cameras (series CVS 3000) and capable of effecting ultra-reliable inspection of every side of the cap, the result is, again, better line efficiency and overall output quality.
To complete the picture, this fair - the last edition of which attracted 160,000 visitors and 2,700 exhibitors from 59 countries - will also be showcasing the TF 70 modular tray former designed by Sacmi Packaging; this machine has won widespread market acclaim thanks to outstanding production flexibility with all tray types.
As the name implies, the machine offers excellent modularity. The different base modules (magazine, press and corner) are used to create the new TF 70 tray former, currently the most competitive, highest-performing solution for corner trays on the market. A major strong point of the solution - in addition to excellent output rates of up to 50 pieces per minute thanks to the dual feel track and other technical devices - is the possibility of working in line with the new stacker, redesigned by Sacmi to keep pace with the outstanding productivity of the new machine and so manage two trays in parallel, up to a maximum length of 800 mm, and make stacks of unlimited height.
The latest solutions from Sacmi also have plenty of other winning features such as, to name just a few, lower maintenance requirements, user-friendliness and fast size changeovers: features that have, over the years, kept us several steps ahead of our closest competitors.