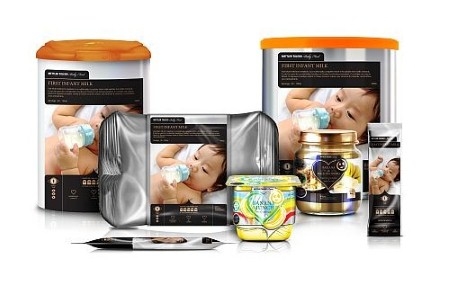
In the past, baby and infant food was prepared at home by their mothers and carers, and it was not until the middle of the 19th century that the first baby foods were manufactured. At first, these were ‘infant formulas’ intended to replace the mother’s milk. The products developed over the years, offering a whole range of new flavours, gradually incorporating cereals, fruits and pureed vegetables. They were considered by many to be better than homemade food which required more preparation time than just opening a jar of ready-to-eat baby food.
For decades, many baby food lines were packaged in glass jars. There were really no alternatives and this type of packaging was ideal for heating and sterilization. However ultimately, safety issues – including breakages leading to pieces of packaging turning up inside the food product – and different lifestyles spurred a change in trends.
Packaging Shift
As we became more mobile, we started to feed our babies ‘on the go’ or outside of our own home. This shift in packaging was defined by a move from glass to plastics. The introduction of flexible packaging such as laminated pouches used for wet food like cold or hot beverages, metallised films for snacks, and retort pouches used as an alternative to cans, transformed baby foods into convenience items. In addition to a marked decrease in breakage risks, the ability to sterilise the product remained intact. Because they were less fragile than glass, they were easier to store, lighter to carry and simple to open; the use of plastics in baby food packaging met the flexibility needs of the contemporary increasingly mobile carer.
There were also benefits to be had for baby food manufacturers as they were able to maintain low production costs as plastic packaging requires less energy to produce, less materials and historically has a lower environmental impact, than say cans or jars. In addition, they carry a lesser risk of the product being compromised through denting/or breaking.
Consumer and Retailer Concerns
No revolution is free of concerns though. Research has shown that plastic-related chemicals and most notably Bisphenol A (BPA) – a raw material used in polycarbonate plastic which is utilised in packaging- can be incredibly harmful to the most vulnerable in our communities. Studies have shown that even low-level exposure to BPA can lead to reproductive harm, early puberty, increased risk of cancer, and depression in teenage girls. Baby bottles containing BPA were banned in 2010, first by the European Union and China and then later by the US Food and Drug Administration in 2012. Furthermore, a 2013 study published by the University of Michigan now suggests a possible link between BPA exposure and childhood obesity. It is thought that children who have a higher level of BPA in their urine could run the risk of facing heart disorders in later life. New safety rules for infant formula will take effect from 1 May 2014, whereby all producers and manufacturers looking for export to China, involved in the process, will undergo an inspection by Chinese authorities prior to approval. In addition, all dairy producers, other than formula milks, exported from the UK must have been approved by Certification and Accreditation Administration (CNCA).
In addition, there is always the concern over product recalls. There have been many well documented cases over the years which were due to contamination and spoilage. Food manufacturers in general aim to avoid those recalls – often born out of packaging problems– that damage brands, resulting in billions of dollars in losses each year. In October 2013, American International Group (AIG) estimated that on average there were 30 class I and II product recalls each week in the food and beverage industry in the US and 22 equivalent recalls in Europe.2
The possible presence of e coli bacteria which causes severe food poisoning or contamination, such as glass shards or metal fragments within the product, can lead to a precautionary recall at best or at worst to a fatality or high profile court case leading to additional costs, loss of sales and profits, not to mention brand damage.
Both the consumer and baby food companies retain their own concerns over the product and the manufacturing process. Consumers – the parents – look for value pricing: safe packaging and the latest technology producing a palatable food product containing crucial nutrients for their infants at an affordable price.
How x-ray technology can overcome these concerns
Any shift in packaging trends must be met with the product inspection technology aimed at ensuring food safety and manufacturing efficiency. X-ray technology meets the baby food packaging requirements most comprehensively. While the use of x-ray technology is mainly for contaminant detection, these increasingly popular systems have additional features for quality control, inventory and weight assessment. The ability to provide quality control of cap closures, fill level monitoring and detecting any product captured in the seals further protects the integrity of the product by preventing any spillage or contamination. The capabilities of the technology apply to all types of packaging – glass jars, metal or composite cans, retort pouches etc. - and put it at the forefront of most detection technologies.
X-ray inspection technology can now address contamination concerns in baby food products with an increased metal detection capability down to a tiny 1.0 mm in glass jars and 1.2 mm in metal cans. In addition, the glass contamination detection capability is currently in the range 2.5mm to 4.0mm depending on container type and size. Glass containers have always presented a challenge in the past. This is because x-rays do not pass through all materials with the same ease, and in the case of glass, the thicker it is, the harder it is for the x-ray to pass through to detect foreign bodies. Latest technology, such as the InspireX R50G is designed to enhance glass contaminant detection in glass packaging at high throughput speeds, i.e. up to 1,200 containers per minute. This is because the system is equipped with an optimised x-ray beam geometry, featuring a single, perpendicular beam that scans the base area, while simultaneously inspecting the side of containers, providing all-round glass-in-glass inspection. This reduces blind spots and optimises detection in the most challenging areas i.e. a thick glass bottomed jar. In addition, the body and neck of the container, plus the cap are all fully imaged on the x-ray detector; ensuring comprehensive inspection and enabling inspection of jar fill level as well. The InspireX R50G offers the complete solution to the manufacturer with the simplest of integration. The unit includes all transfer points with the reject collection table, and simply locates alongside the manufacturer’s existing conveyor without any need for costly product spacing.
Looking to the future
Despite all the concerns, the baby food industry is doing well. According to market research, analysts forecast the Global Baby Food and Formula market to grow at a compounded annual rate of 5.4 percent over the period 2012-20163. One of the key factors stated in the report is the growing urbanization in developing countries where disposable income is increasing. However the declining birth rates in more mature markets and the possibility that mothers may decide to return to breastfeeding their babies, might stunt the growth of infant formulas and give baby food manufacturers some new challenges.
Modern x-ray technology inspection systems provide a solution to the concerns of both baby food manufacturers and the buying public. By providing the most thorough contaminant detection, which in turn reduces the risk of product recall, this energy efficient technology helps to protect the infant, manufacturing businesses, brands and potentially market shares. Safe packaging ensures the secure delivery of a crucial food product to the most vulnerable members of our communities and provides a bit of solace to their ever-anxious parents.