Before investing in labeling equipment, brand owners must decide what they want out of their machinery, says Mike Soloway, labeling product manager at Krones Inc., Franklin, Wis. “Can this machine handle my products and rates?; Can I afford the maintenance and repairs?; What are the changeover costs?; What is the changeover time?”
Because each customer is different, each requirement is different and could require customized solutions, he explains.
“Each base machine model uses the same primary components, but the product handling and media handling components are built to the customer’s specific needs, including possible future needs,” he says. “When new products are introduced into the system at a later date, we can simply provide a new set of change parts to accommodate that new product.”
Justin Slarks, director of marketing at Little Rock, Ark.-based Sleeve Seal, emphasizes how “repeatable performance” is a main attribute for the company’s customers when selecting labeling machinery.
“Our customers typically have basic needs that boil down to ‘repeatable performance at X speed,’” he says. “Sometimes they have very, very specific and complicated needs, but the bottom line always is repeatable performance at X speed. In either case, Sleeve Seal is able to offer solutions with high efficiencies and affordable change parts.”
Certain considerations also should be taken into account when applying labels to different types of packages based on material type, size, shape and more.
According to Krones’ Soloway, manufacturers should ask: “Is the container cylindrical or shaped?; Is it wet or dry?; What is the container made of?; What is the temperature of the bottle and contents?; Are we labeling in difficult areas like the bottle shoulder, lid, recessed areas, etc.?; What is the shape of the label?; Will we need to integrate any coding devices?”
After manufacturers understand what they are looking for, they then can decide which machinery will best suit their needs, he says.
Technological advances also should be taken into consideration. “As machines advance, there are new possibilities for shapes and graphics,” Sleeve Seal’s Slarks says. “We are seeing more non-round containers that need to be more label-oriented and applied at certain speeds.”
Accurate application
When it comes to selecting labeling equipment, manufacturers want machines that are dependable and accurate, experts note. Sleeve Seal engineers its machines to be mechanically simple, but accurate to ensure repeatable application performance over thousands of hours of run time, Slarks says.
“We also use the best quality, most advanced Allen Bradley controls and have a team of very talented programmers that make the magic happen,” he says.
To ensure the equipment applies labels properly, systematic experience is key, Krones’ Soloway says. “Krones produces not only labeling machines, but complete bottling lines including brewhouses and processing equipment, blow molding equipment, inspection equipment, dry end equipment and the software and systems that drive the complete lines.
“We understand how all the pieces need to work with each other within the line,” he continues. “When we quote a labeling machine, we document every single container and label that will be used on that machine and consider any future containers that may be needed later.”
For rare exceptions, when the company sees truly unique applications, Krones’ team of engineers will evaluate each application on a case-by-case basis and build a new machine, Soloway says. “Our engineers will test the customer’s samples and then provide the best solution. Once the machine is built, we offer a Factory Acceptance Test, which allows the customer to inspect and test every aspect of the machine before it ships,” he adds.
Although SKU proliferation has placed a greater emphasis on flexibility, some manufacturers want to run the same product the same way a million times, Sleeve Seal’s Slarks says. For those particular customers, the need for flexible machinery isn’t as important, he adds.
Likewise, Krones’ Soloway explains that some customers have a limited number of products that they run on their machines and don’t require a lot of flexibility. These labeling needs enable companies to keep their capital expenses minimized, he says.
On the other hand, other companies like contract packagers require much more flexibility because their customers are constantly introducing new and different product shapes and sizes, he says. That level of flexibility can be satisfied using modular labeling systems.
“Our modular labeling systems allow the customer to change not only the product being labeled, but also the labeling technology itself,” Soloway explains. “For example, we can run cold-glue labels for one product and then easily swap out the cold-glue label aggregate with another technology like hot melt or pressure sensitive to run a different labeling technology on the same machine.”
Krones’ modular systems use servo drives for all the main components including the container table, the infeed screw, the infeed and discharge starwheels and the bottle plates. Servo technology provides very accurate product handling and reduces the wear and tear traditionally seen with gear and belt driven components, he adds.
“Servo driven bottle plates allow us to customize the rotation of each bottle during the labeling process so we can orient, label and inspect each bottle as efficiently as possible,” Soloway says. “That modular technology has just been redesigned and our new ErgoModul series is easier and more cost-efficient than the previous generations.”
Another example of ultra-flexible labeling machinery is manufactured by Parma, Italy based-Sidel Group. The company recently launched EvoDECO Multi, its most flexible labeling solution to date. The EvoDECO Multi offers a standardized carousel that can be equipped with up to four different labeling technologies: roll-fed, self-adhesive, cold glue and hot melt, the company said in a statement.
“This allows manufacturers to set up the machine for their unique labeling needs, as they can easily apply several types of labels to different types of containers and packaging of varying formats and dimensions,” it added.
Fairfield, N.J.-based HERMA US Inc. also is addressing flexible labeling needs with its HERMA 400 Label Applicator. “The HERMA 400 can apply any type of adhesive label to virtually any type, size or shape of product or package,” the company said in a statement.
Sustainable labelers
As packaging becomes more sustainable, OEMs have to innovate their equipment to follow suit. “New materials and adhesives constantly are being developed to improve the recyclability of the containers and labels, and Krones has been able to adapt its machines to work with those new materials as they are introduced,” Soloway explains.
From a machine standpoint, Krones designs all of its machines to be as energy efficient as possible and also to use the least amount of consumables as possible, he continues.
Enviro, an independent organization, evaluates Krones’ machines to ensure that are certified energy efficient and produced in an environmentally friendly way, Soloway says.
Similarly, Sleeve Seal’s Slarks notes that thin film is a new sustainability trend that requires more advanced equipment. “With film as thin as 25 microns, manufacturers are able to save sustainably due to simply having more impressions per roll,” he says. “Less raw materials are needed and the impact of shipping the same number of label impressions changes dramatically so more manufacturers are looking for thin, recyclable film.”
The aforementioned EvoDECO Multi from Sidel also was created with sustainability in mind. The EvoDECO Roll-Fed labeler contains an integrated glue tank, patented vertical melter and heating control, which then melts the glue on demand and is circulated always at a precise temperature in smaller quantities, increasing the label quality application, the company said.
“This allows for reduced consumption of glue and avoids glue degradation, glue filament and glue splashing, for overall improved sustainability,” it added.
Despite the technological advances of today’s labeling machines, pre-printed films can present challenges. Krones’ Soloway notes that many customers are moving away from traditional cans and bottles and moving to flexible packages, which are made from pre-printed film. “Anything that is pre-printed, whether it’s a bottle or a pouch, is inherently limiting because that pre-printed information cannot change,” he says.
Changes to the artwork, even something as simple as a different ingredient, can result in those pre-printed packages being discarded, he explains.
However, newer digital technologies currently being developed will allow those images to be printed as the product is being packaged, therefore, reducing the amount of waste, Soloway adds.
Sleeve Seal’s Slarks notes that labeling complexities are on the rise because good operators are hard to find. “Sleeve Seal is engineering its machinery for ease of use and to take some of the operator input out of the equation,” he says. “Ultimately, the best machine won’t work if the operator is subpar.”
Krones’ Soloway expects digital container decoration to become widely popular in the coming years. Digital printing can decorate containers in areas that are impossible to label, such as recessed areas in bottles, he says.
Bottles can be designed to take advantage of this benefit and the artwork can be printed to enhance the unique features of the bottle design, he adds.
“In addition, digital printing technologies allows images that require no paper for film media and each bottle can be printed with different variable data,” Soloway says.
Sleeve Seal’s Slarks notes that in the future, labeling equipment companies should continue to innovate their products for speed, durability and repeated performance.
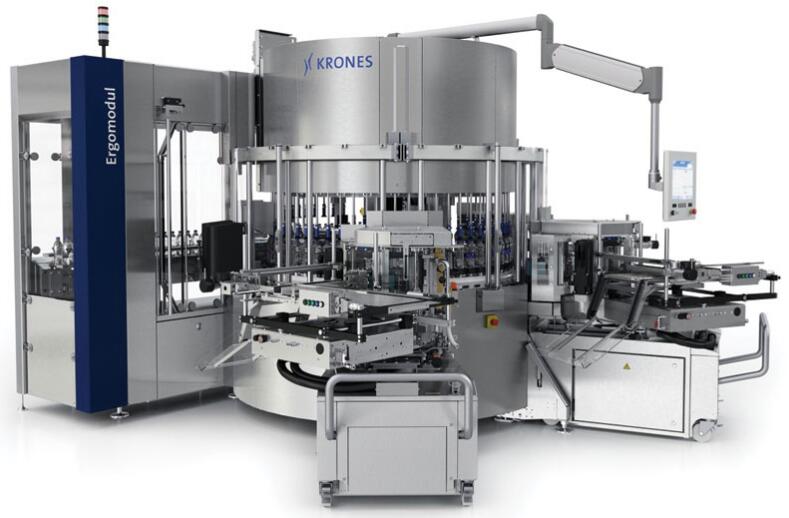
Source:www.bevindustry.com