S
witzerland-based Interroll installed a push back system with 700 pallet positions featuring 3-, 5- and 7-pallet-deep lanes in one of Dole Food’s workshops in Korea. With this new system, Dole will be able to increase their storage by 30% and reduce energy consumption by 20%.
“In the past, we used drive-in rack systems, which not only require comprehensive forklift driver training, but also bring challenges in terms of safety in the working environment,” says Nam-Kuk Kim, director of Dole Korea. “Interroll push back system is very user-friendly. We just need to put in or get out the pallets at the neck or the neck after the first pallet and don’t need to drive into the rack, which can save us an average 25% of our time.”
Interroll push back system was designed as a dedicated LIFO system, which can save a lot of space and achieve 80-95% occupancy utilization. While unloading product available in front position, there is no need for the operator to enter the rack, which can provide maximum safety.
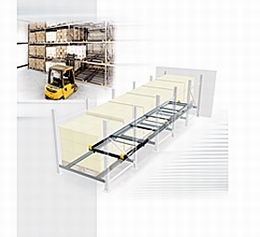
“In the past, we used drive-in rack systems, which not only require comprehensive forklift driver training, but also bring challenges in terms of safety in the working environment,” says Nam-Kuk Kim, director of Dole Korea. “Interroll push back system is very user-friendly. We just need to put in or get out the pallets at the neck or the neck after the first pallet and don’t need to drive into the rack, which can save us an average 25% of our time.”
Interroll push back system was designed as a dedicated LIFO system, which can save a lot of space and achieve 80-95% occupancy utilization. While unloading product available in front position, there is no need for the operator to enter the rack, which can provide maximum safety.