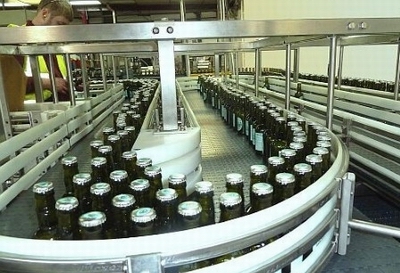
During Thomas Hardy’s recent upgrade to the end of line packaging system at the Kendal site, where a new shrinkwrapper was installed, there was a requirement to modify the bottle conveyors feeding the new machine. As a contract packer, the company’s requirement to handle a wide range of bottles and packaging formats had resulted in the new shrinkwrapper occupying a lot of the available floor space. With the compact nature of the bottling line posing a challenge to installation changes Thomas Hardy approached Walsall Engineering to consider the optimum design solution.
Walsall Engineering’s solution involved the design and installation of a new bottle conveying system, from the labeller discharge to the infeed of the shrinkwrapper, with a bottle recirculation at the heart of it. The main advantage of the recirculation system was to provide a compact bottle accumulation solution where space was at a premium. The layout as designed by Walsall Engineering was a perfect fit for Thomas Hardy.
Working in close co-operation with Thomas Hardy and the shrinkwrappper supplier, the old machine and conveyors were removed as soon as the last pack came off the line. After that the new conveyors and shrinkwrapper were installed over a very short period with production starting immediately after completion of installation. The end of line packaging system was soon producing good levels of production over a wide range of bottle sizes with frequent changeovers. The guide rail system on the bottle conveyors was purpose designed to suit the full range of bottles and accommodate the frequent size changes.