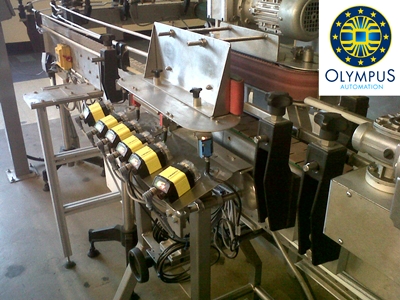
The factory was using a label verification system where one element of the previous system could only read ladder barcodes and although a separate system was created to read the picket fence barcodes, the readers could not cope with the speed of production. Heinz were keen to upgrade to a more reliable system which could achieve 100% read rates thereby eliminating any risk of packaging errors, and looked to Olympus Automation to install a barcode reading solution to achieve complete code reading accuracy.
Based in Peterborough, Olympus Automation is a leader in process and automation systems, providing world class turnkey solutions to the food, beverage and pharmaceutical industries. Working alongside Cognex, Olympus selected the DataMan 302X image-based barcode reader which, given its advanced functionality, would allow all images to be seen in real time and therefore establish if a code had been read or not. In addition to meeting the requirements for 1-D code reading, the DataMan 302 readers are able to read new 2D codes planned for use on the cans in the near future.
The high speed production line runs at 97 cans per minute, and in order to read the picket fence 1-D barcode on the round can, each unit has to be rotated. To cope with the convex structure and reflective surface, six DataMan 302X readers are placed in a row along the can turner. As the can is rotated through 360 degrees, each reader is triggered in three batches of two. This process results in at least two of the readers being able to read the code on each can.
If incorrect barcodes or ‘no reads’ are detected, alarm beacons and display screens alert the operators who will stop the line and clear the defective product to ensure no incorrect can continues to the packaging area.
Reporting for read rates is generated as part of the standard Olympus Automation Autocoding system, allowing for easy monitoring of production performance. The system also links in to the site’s Domino inkjet printers and Markam case printers to ensure the correct dates are printed on each pack, ready for shipment.
The key benefits of the system have been:
- elimination of false line stoppages due to ‘no reads’
- prevention of incorrect tins being packed
- print control to ensure the correct dates are applied.
Robin Sandman, Engineering Manager at Heinz commented, “Heinz chose Olympus Automation and Cognex to deliver their Autocoding system because they were the only suppliers we reviewed to offer 100% read rates on products. The integrated quality checks on the Autocoding system and Olympus’ ability to offer 24 hour support have added significant value to the business.”