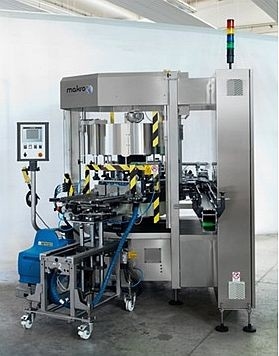
Matthew Orme commented, ”We are very proud of our product, not only the quality of the water but we also take great pride in our packaging. The glass bottles are ideal for the dining table at home, in restaurants and hotels and our PET variants are especially suitable for leisure clubs, spas, cruise ships, airlines, professional kitchens and retailers. We bottle 330ml to 1 litre in glass and 330ml to 2 litre in PET, so when we were looking to up-grade our labeller, the Makro modular machine construction concept seemed perfect for our purposes as it offers us complete flexibility both now and in the future.”
Richard Portman, Managing Director of Makro Labelling UK said, “Wenlock at present have an immediate requirement for hot melt label application and in the future for self adhesive labelling; therefore we will be providing them with a Makro Mak 3 24-platform base machine initially equipped with a holt melt labelling station.
The machine has the provision to accommodate up to 4 labelling stations, therefore giving Wenlock the future possibility to interchange the Hot Melt labelling stations with three self-adhesive stations for their future PSL labelling requirement. The machine will be supplied with the new design Makro adjustable geometry starwheel type changeparts, which are specifically designed to reduce the number of changeover parts required when handling many different bottle formats. The machine will be supplied to label the eleven PET formats and three glass formats.
Matthew really understands the concept of the flexibility of the Makro offering in that what is required in his production now may not be the case in the future, so when his production requirements change it is then a simple matter of just connecting different type labelling stations to alter the label application capability of the machine and not having to invest in a complete new labelling machine. This modular machine concept made it an easy decision for Matthew as it took away any concerns about whether his investment in a new labeller was not only for a machine capable of satisfying his immediate production needs but also to future-proof his investment regarding possible different production labelling requirements.”
The new Makro Mak 3 is due for installation in May.