Usually, prepared salads are packaged in OPP, which cannot currently be recycled in the UK. PE, on the other hand, can be recycled into carrier bags as well as long-life products such as park benches, bollards and waste bins.
Whilst OPP bags could be produced using a conventional heat sealer, the same sealing technology could not be used for thicker PE films - instead, historically, an impulse sealing head was required. The recent development of heat-sealable PE films has eliminated the need for two different sealing modules when running OPP and PE, but ultrasonics has emerged as the sealing technology for creating high integrity seals on both substrates. Latest generation bag makers such as ILAPAK’s Vegatronic 6000 can seal everything from laminated films to PE and LDPE films ultrasonically.
ILAPAK UK estimates that one third of all VFFS (vertical form fill seal) packaging machines in the salad and cut leaf industry field are now equipped with ultrasonics, and predicts that this figure will rise as other retailers and producers follow Tesco’s example and switch to PE films.
“The ability to add claims such as ‘fully recyclable packaging’ to the front of salad packs is a major advantage in today’s increasingly sustainability-conscious market. So too is the ability to claim reductions of up to 10% film waste, 20% film usage and 30% energy consumption - all of which can realistically be achieved with ultrasonics,” notesTony McDonald, Sales and Marketing Manager at ILAPAK UK. “Whilst companies can use conventional heat sealers to produce bags from PE film, for environmental packaging initiatives to have real substance, ultrasonics is the only truly sustainable sealing technology.”
The overriding reason for investing in ultrasonics is to eliminate leaky seals; unlike conventional heat sealing methods, ultrasonics can seal through any leaves which may have accidentally been deposited in the seal area and this leads to huge advantages for economics and the environment. Producers can reduce their ‘rework’ rate from an industry average of 8 to 10% to less than 1%. Put into more practical terms, for every tonne of plastic that is made into bags, 100kg of plastic ends up as waste after being deemed unfit for purpose due to seal issues. This unnecessary waste can be completely eliminated by using ultrasonic sealing.
Besides slashing leaky bag and rework rates, ultrasonics yields film savings of up to 20% owing to a narrower seal area, and energy savings of up to 30% compared to traditional heat seal technology.
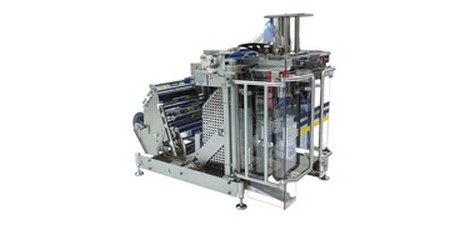
ILAPAK was one of the pioneers of ultrasonic sealing, and its versatile Vegatronic 6000 bagger has become a reference for the salad industry, owing to its ultra-hygienic construction and fast changeover capabilities.
Operating at speeds of up to 80 cycles per minute thanks to digital servo drives, the continuous motion bagger can produce packs of up to 300mm in width from virtually any film.
Open frame design allows the operator to see right through the machine to view the film path and alignment and complete IP65 protection enables full wash down capability.