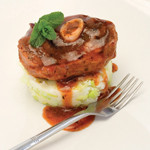
Britain may be officially 'out of recession' but tough trading conditions continue and any capital expenditure by processors requires immediate return on investment, while production lines must be adaptable to meet shifting market demands.
Developments in packaging production processes from coding systems to packing case erectors and tray sealers are offering processors enhanced levels of flexibility, as well as improving efficiency and cutting wastage with the attendant boost to returns and environmental performance.
"There have been great developments in meat and poultry packaging, but now emphasis is on flexibility and consistency," says Peter Smith, md of Gilbert's Foods, a Lancashire-based manufacturer of lamb, beef, pork, chicken and duck dishes.
"Products need to be visually appealing too. Our products go into retail and foodservice so packaging needs to be presentable both to chefs and consumers, and meet their cooking needs, while retaining the quality and flavour of the overall dish.
"When we invest in new packaging production processes, we need to ensure product quality is retained and that flavour is in no way affected by the packaging."
Traceability vital
A further prerequisite is traceability, which can easily go awry without the proper systems in place. "Processors can't afford to pack a wrong product, mix up labels, pile up fresh inventory or ship the wrong product to the wrong customers," says Terry Starkey, marketing consultant at Marel. "Marel's retail pack handling and collation systems provide processors with traceability from pack to box to pallet."
Marel supplies robot portion loading and batching, multi-head weighing, check-weighing, weigh-price labelling and packing stations, and packing and dispatch information management systems.
The Marel TG9 tray grader and TD9 tray diverter receive weight, price and pack information from a WPL9000 weigh-price labeller or barcode scanner on the in-feed; using the information to grade product trays to collate fixed count, fixed weight or combination boxes of packs with totalised labels.
Marel's Innova software then tracks all pack and batch information, allowing non-conforming or damaged packs to be quickly and easily removed from a batch by operators and replaced by re-ordered packs from the product flow.
Innova also tracks independent totals at box, pallet and job level, including item, weight and price, with labels printed and registered by Innova or another production management system.
Flexibility and avoiding wastage were key determinants for Pork Farms' recent selection of Allen Coding Systems' 4ACC off-line carton coder to replace an old machine at its factory in Shaftesbury; handling packaging of products such as Snackpots for Tesco Southern Fried Chicken and its Mini (Scotch) Eggs.
"The 4ACC has resolved the issue of code drift and wastage that we were experiencing with our previous labelling system, which had reached the end of its life span," says Simon Greenwood, chief engineer at Pork Farms. "The best features of this Allen machine are its ease of use and ability to facilitate quick changeovers, enabling it to deal with numerous product changes each day."
Operating at 40 to 50 cartons a minute, the 4ACC prints Pork Farms' date codes onto a variety of different cardboard packaging while offering a choice of coding options, including the star wheel type code and intermittent thermal transfer.
Long-term investment
For Interfood, flexibility is vital for processors seeking long-term returns from capital investment.
"When capital investment is being made in machines, processors are looking to maximise how they can be used," says Rob Allen, product manager at Interfood.
Interfood is the UK representative of Buhmann, a German specialist in packing machines for the food processing industry. Its lines include a range of case erectors offering the capacity to produce display cases and wrap-around cases from flat, non pre-glued blanks on the same machine.
"Similarly, the systems are available for products to be automatically loaded flat or stood up in the cases or crates, again within a single machine," says Allen. "Processors want to know that their investment is for the long term, capable of handling their current requirements but also future-proofed should those requirements change through the development of different operations and new products."
Meanwhile, skin packaging developments offering greater versatility were the focus of a Fresh Innovation workshop recently hosted by Linpac Packaging, G Mondini and Bemis, respectively manufacturers of multi-material packaging, tray skin packaging machinery, and films.
Mondini's Trave 340 sealing machine was demonstrated, working with Linpac's new range of VSP trays and Bemis SkinTite film.
"Traditional skin packaging options, whilst offering extended product shelf-life, do not always have the greatest shelf appeal and also present the retailer with challenges in terms of branding and shelf space efficiency," says Joanna Stephenson, vice president of marketing and innovation at Linpac.
"The solution we have put together addresses all of these issues but also offers the packer a flexible and highly efficient packaging line that is suitable for both high and low run lengths. It gives the retailers a great looking pack which can be attractively branded and displayed shingled, vertical or by the inclusion of a Euroslot, hung to maximise shelf space efficiency."
The same machine can skin pack a normal tray for sliced and cooked meats, protruding skin packs for steaks, chops and chicken breasts and super protruding for joints and whole chickens, while shelf-life for meat can be extended by up to three days.
Level of automation
While the trend towards increased automation is continuing, the level used is very much specific to individual processor demands.
Marel believes processors should use "as much automation as possible, but not only at the end of the line", says Starkey. "At the end of the day, automation is essential to cutting costs and getting product into the pack hygienically and as perfectly as possible."
For Interfood: "Maintaining the lowest cost of production is, quite naturally, a focus for meat and poultry processors, so automation is, and will remain, key," says Allen. "Production is driven by cost, quality and efficiency and is really what all the major processors are looking for. By adopting automated processes and removing or minimising the need for human intervention, a repeatable and consistent product process can be achieved, driving increased efficiency and control of product quality."
Green issues rule
Eco packaging may have lost its clout for cash-strapped consumers but, for processors and retailers, can cut costs and wastage and help meet legislative targets for carbon footprint reduction.
Among competitive claims for the Eclipse range of tray sealers from Packaging Automation (PA), is the 'massive' savings in running costs and carbon footprint in comparison with pneumatic systems.
Laying claim to 'new standards for reliability, ruggedness and return on investment', Eclipse lines have been installed at a number of poultry packing sites, achieving levels of below 0.5% residual oxygen without the aid of a costly full vacuum system.
For Interfood: "Attention is also being paid to the costs of the packaging materials themselves, further driven by the need for an approach to packaging which is environmentally responsible and recognises that excess packaging is becoming less and less acceptable," says Interfood product manager Rob Allen.
"Automated packaging machines are now available which can significantly reduce the footprint of the carton blanks, potentially reducing material costs by up to 30% when compared to conventional systems, with the added advantage that they leave clear space on all sides of the carton for graphics and shelf branding without the need for perforations."
Gilbert's Foods also looks for cost savings tied in to environmental-friendly production. "The meat processing industry as a whole is constantly striving to be more environmentally friendly," says Gilbert's Foods' md Peter Smith.
"Earlier this year, the Department for Environment, Food and Rural Affairs (DEFRA) announced its new recycling recovery targets for 20132017, and we will do everything to ensure we recycle as much material as we can to support DEFRA in meeting its targets."
Gilbert's Foods views ambient meat and poultry packaging as the way to go. "Packaging and storing products under ambient temperatures requires no energy costs for storage; therefore is more environmentally friendly than frozen or chilled foods," says Smith.