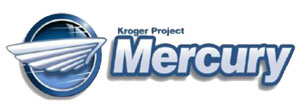
The Cincinnati-based retailer assembled a team of specialists at the GS1 US Connect 2013 conference here to prepare its suppliers for the project — a radical transformation in the way they will be delivering product information to Kroger, and the way Kroger will be managing the data.
“This is the largest project our corporation has ever taken on from a financial and HR standpoint,” said Dave Schmitt, director of Project Mercury. He expects it to positively impact customer service, speed-to-market, among other areas.
Kroger is unveiling the program in phases over the next three years. The pilot phase kicked off in April as suppliers of the first nine classes began testing the system.
The classes include packaged cheese, salad dressing, breakfast sausage, baby HBC, coffee filters, bagged salad mix, air care, paper towels and packaged deli meat. Kroger plans to go live with those products in September.
In the spring of 2014, Kroger will continue with the next 120 classes, which are listed on Kroger’s customer page at www.1sync.org; ultimately the company plans to convert 670 classes to the program.
Kroger is asking suppliers to supply about 150 “attributes” — features ranging from size and weight to nutritional components – for each item; the attributes list is also is also available on Kroger’s customer page at www.1sync.org.
Under Project Mercury, suppliers will deliver data on new and existing items to Kroger via the preferred mechanism, the Global Data Synchronization Network (GDSN), or via the retailer’s vendor item portal. Kroger will manage the data in a still-developing master data management repository.