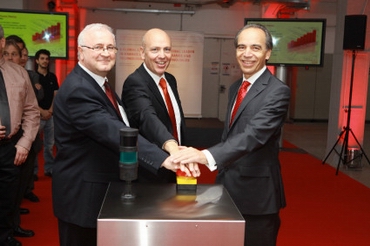
At present the production plant in Vienna supplies products to 14 countries in Central and Eastern Europe. The biggest share of the manufactured brand-name goods are fabric softeners (Silan), heavy-duty detergents (Persil, Dixan, Weißer Riese) as well as hand dishwashing detergents (Pril). “With the coming on stream of the new production lines for Clin window cleaners, we successfully concluded the conversion of the Vienna plant to a purely liquid product site”, says Günter Thumser, President of Henkel Central Eastern Europe. “However, we are resolutely moving ahead with our investments. In the future we aim to successively expand our fabric softener production.”
Wolfgang Weber, Head of Production Control Core Central Eastern Europe, adds: “Each year we invest about 10 million Euros at the site and focus on modern high performance facilities. Above all, Vienna benefits from the extensive technical know-how of its employees.” Creativity is essential in order to achieve the desired objective of reducing resource consumption at the plant. The conversion to LED lighting, the coming on stream of a combined heat and power plant and new chemical formulas requiring less energy in the production process are examples of recently implemented measures in this regard. “In the period 2010 to 2012, we succeeded in cutting water consumption by 17 percent and energy consumption by 13 percent for each ton manufactured”, Wolfgang Weber says.