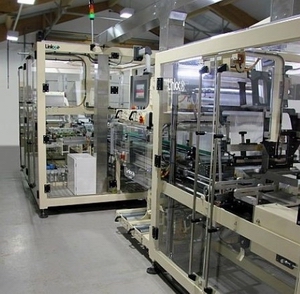
A key feature of the new machine is its high operating speed of 28 cycles per minute, which Linkx has achieved by making effective use of the latest servo drive and automation technologies. Not only does this high speed maximise the throughput of the machine, it also allows it to efficiently perform the 4 x 1 collation that is needed for the latest slim shelf-ready packs, which are becoming increasingly popular with retailers.
A further development provided by the new machine is automatic splicing for the rolls of shrink-wrap film. This is achieved by a new design for the film cradles, which means that they can be withdrawn from the machine to allow easy access.
Throughout the development and construction of the new machine, the engineers at Linkx Systems worked closely with their counterparts to devise refinements that would optimise every aspect of the machine’s operation. As a result, the new machine is significantly more ergonomic and is even easier to use than its predecessor.
Like the original machine, the new one receives the cartons of teabags from the production line, turns them on end, collates them on a tray, glues the tray and then provides an overall shrink wrap. It handles four different sizes of carton, which between them need 11 different collation patterns. Size changes are fast and highly automated, eliminating the need for manual adjustment and ensuring that machine up time is maximised.