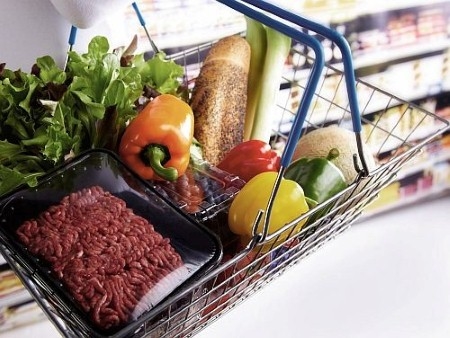
Organised by ELIPSO, the French Plastic and Flexible Packaging Association, and IK, the German Plastics Packaging Association, PackTheFuture 2014 focuses on promoting the innovative and creative potential of plastic packaging to the public.
Rfresh Elite claimed its award in the Ecodesign category in which judges considered factors such as recyclability, source reduction and weight reduction.
The super lightweight, mono-material Rfresh Elite tray uses a new unique, patented, sealant on the tray flange to create a secure seal with the lidding film, removing the need for the industry standard laminated PE base film and creating a crystal clear tray which is 100% recyclable at the end of its service life - a breakthrough in tray packaging design.
The trays are manufactured from up to 95% rPET, which has passed through LINPAC Packaging’s food grade super cleaning system to ensure it is entirely food safe and have been developed in conjunction with the company’s Project LIFE (LIghtweighting For Excellence) initiative which has been implemented to significantly reduce the overall weight and carbon footprint of LINPAC trays, whilst ensuring that they maintain excellent performance and integrity.
Director of Innovation at LINPAC, Alan Davey, collected the award in Germany on May 13. He said: “The Rfresh Elite tray offers superior efficiency and sustainability features for meat and poultry packers, and indeed helps the entire food supply chain reduce its carbon footprint and costs in handling and logistics.
“The removal of the PE base film, normally applied to facilitate tray sealed lidding, reduces the tray weight by up to 3% in addition to the 10% reduction delivered through the lightweighting programme. This means that the carbon footprint of an Rfresh Elite tray is typically 5% less than the average rPET/PE tray.
“We are extremely pleased to have received a PackTheFuture award and hope it will be the first award of many for our Rfresh Elite tray. It took two years for the innovation team at LINPAC to develop the unique sealant which is completely food safe and has proved effective in reducing leaking packs.”
The ingenious sealant can be removed in the hot wash process employed by Europe’s PET recycling companies meaning a recycled Rfresh Elite tray will yield 100% crystal clear PET after recycling, in the same way as a clear bottle, and allows trays to enter and benefit the entire closed loop rPET supply chain.
The sealant on the tray flange is opaque, only turning clear after the lidding film has been heat sealed onto the tray. This gives a very strong visual check for the packer processors on the seal integrity of the pack. Something they cannot see currently.
The tray has the strongest seal strength in its class – there is a 60% improvement in burst test strength and a 24% improvement in vacuum chamber testing compared to standard PET/PE packs.
Rfresh Elite trays also require significantly lower levels of heat for sealing. This reduces the packers’ machine energy consumption by around 15%, lowering their overall carbon footprint and in addition, the packaging is not adversely affected by the heat during the sealing cycle. This removes the risk of rolled flanges, hour glass shape trays or poor lid film visuals which sometimes affect other lightweight PET/PE trays.
In addition, seal dwell times are reduced by up to 50% compared to standard rPET and PP trays; some machines have achieved seal time savings in the region of 0.5 seconds. This means packers can increase their throughput by around 10% which translates to production of an extra 10 packs per minute or 12,000 packs per day.