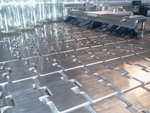
The company was speaking as it launched a ‘sustainable’ lubricant, GlassLube 2.0, for use with glass bottles on a stainless steel packaging conveyor.
The product is based on natural materials from renewable sources, and Dry Lube said it completely removes the need to lubricate packaging lines with soap and water.
Dry Lube warned that – as concerns about scarce water supplies moved up the agenda – food and beverage companies (the firm counts some blue-chip clients) were becoming visible heavy users.
Another more direct risk was that local authorities could shut off supplies to foreign investment firms, or sharply raise the price of water, the firm added.
Major South American trial
Julia Heyse from Dry Lube told BeverageDaily.com that her firm’s precursor to GlassLube 2.0 was called GNS, and was based on similar ingredients.
“But we have optimized it further. GlassLube 2.0 has a better hygienic outcome, while the viscosity is lower, which means it can be spread about more precisely,” she explained.
Dry Lube’s lubricant is 100% water, PTFE and silicone free, and the firm said recent trials for a leading brewery in South America (producing 63,000 bottles/hour) showed positive results.
Packaging line efficiency improved by 15%, while motor temperatures dropped 7%, and the brewer achieved water savings of 9.6m liters each year, Dry Lube claimed.
More generally, using its lubricant cut water usage and effluent disposal from the lubricant process by 99%, Dry Lube said, while the technology had cut the carbon footprint of Europe’s largest soft drinks manufacturing site had been reduced by around 200 tonnes of CO2 per year.
Coca-Cola Enterprises adoptation
Although not cited as such in the Dry Lube statement, Coca-Cola Enterprises’ site in Wakefield is the largest soft drink site by volume in Europe, and CCE is named by the firm as a client elsewhere.
Dry Lube also touts electricity saving given rising electricity prices for EU industrial consumers, and also safety advantages, since 90% of UK work slips and trips occurred when floors were wet.
Heyse said that dry lubrication technology first emerged in around 2003, and despite growing uptake still faced an acceptance threshold within the industry.
“I can’t give you a precise number, but wet lubrication is dominating the industry, which is quite a surprise given the benefits of our technology.
“On one hand I think many people don’t know that the technology exists, or if they do, many of our competitors only provided semi-good solutions in the past, which only worked imperfectly.
“So there are a lot of engineers in the field who have doubts about dry lubrication, which they shouldn’t have as we really have the expertise as specialists in this field.”
Rising demand
Asked where in the world the technology was taking off, she said: “Look at countries such as South Africa and South America, as water gets more scarce, there is rising demand for dry lubrication.”
“In Asia and all over the world there is interest. Sometimes with bigger corporate companies there is more of a procurement issue, they like to give contracts to one or two suppliers in that region.
“One of our constraints now is that is that a head office wants one or two suppliers, and then local demand cannot be answered as such.”