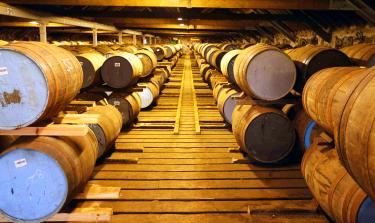
The production of Scotch whisky has evolved over more than 500 years and is steeped in tradition. It is also a big business, generating £4 billion (US$6 billion) a year in exports — a quarter of all Britain’s food and drink sales abroad.
New distilleries are being built to meet demand from more than 200 countries around the world, including new markets in Asia, Latin America and the Middle East. Family-run, centuries-old distilleries are trying to minimize operational costs.
Most distilleries in Scotland have relied on heavy fuel oil to generate heat for distilling processes, but biomass, such as wood, plant-based material or organic waste, is now an increasingly attractive and reliable option.
“As we expand capacity, biomass will be an integral part of what we are doing going forward,” said Gerry O’Hagan, operational excellence director of spirits and wine for Diageo PLC, the world’s biggest spirits company.
In the whisky-making heartland of Speyside in northeast Scotland, Diageo opened a £45 million distillery four years ago at Roseisle. Barley fields surround the modern industrial building, with glistening glass walls enclosing huge copper stills.
The distillery, which has no access to a gas line, produces 10.5 million liters a year, which is matured for a minimum of three years before being used in brands such as Johnnie Walker.
REDUCED EMISSIONS
Diageo has spent £17 million on a bioenergy plant with a capacity of 8 to 10 megawatts (MW), or enough to power up to 10,000 homes. The distillery gets more than half of its energy from the biomass plant, which also saves about 10,000 tonnes of carbon dioxide emissions a year.
The plant generates energy by burning byproducts of the distilling process such as spent grains, which would otherwise have been sent to farmers for use in animal feed.
The rest of the distillery’s energy comes from burning heavy fuel oil, which is more harmful to the environment and more expensive. Diageo hopes to increase renewable energy to about 80 percent of the plant’s total by mixing its byproducts with wood pellets.
“There is concern about energy [prices] in the long term and about how we can make ourselves as self-sufficient as we possibly can,” O’Hagan said.
Diageo has also installed a bigger, 30MW bioenergy plant at its Cameronbridge distillery near Edinburgh; is building another plant at its Glendullan distillery in Speyside; and has plans for a third at a new malt whisky distillery, also in Speyside.
“There are around 20 new distillery projects at the moment. Some of them are tiny, but around half are in the planning stage, and many of them are asking about biomass,” said Julie Hesketh-Laird, director of operation and technical affairs at the Scottish Whisky Association.
“It makes good business to keep your energy costs down,” she added.
Today’s distillers have to contend with volatile energy and commodity prices; often uncertain barley harvest yields due to more extreme weather patterns; and customers such as supermarkets that are scrutinizing their green credentials.
North Sea oil production is in decline, and the debate around Scottish independence has raised the question of who might control the US$2.5 trillion of reserves, which adds to uncertainty about future oil supply.
“There is a question mark about heavy oil supply and how much there is left. As an industry we don’t look at tomorrow or next week, we are looking at 12, 15 or 20 years down the line,” said Graham Eunson, general manager of the smaller Tomatin distillery.
SMALLER PLAYERS
Smaller, more traditional distilleries must rely on government subsidies to make the economics of biomass work. Under a scheme called the Renewable Heat Incentive (RHI), the government rewards the use of renewable energy technology.
Remote Tomatin, 315m above sea level on the eastern edge of the Monadhliath Mountains, produces 2.5 million liters a year. Two-thirds of its more than 40-strong work force live in housing on its 57-hectare estate.
The plant is one of the oldest distilleries in Scotland, with whisky thought to have been made at the site as early as the 16th century. However, it has experienced troubled times, going into liquidation in the 1980s before being bought by Japanese sake maker Takara Shuzo Co.
Tomatin, which has no gas links, had relied on fuel oil until last year, when it installed a 4MW biomass boiler that burns wood pellets.
“To make that sort of investment on an unknown fuel source is a gamble. It is still perceived as a risk, because if it doesn’t work, it’s an expensive mistake,” Eunson said.
“When we learnt we could get RHI payments, it was a key driver. As much as would love to be the most environmentally friendly firm, if the price of production [from biomass] is twice as high, it would put us at a huge disadvantage,” he said.
Biomass has now replaced 82 percent of the fuel oil it would have used, and Tomatin has cut its annual fuel costs by a third.
Furthermore, “if something happens which impacts the oil price, we are now safeguarded from that to a certain extent,” Eunson said.