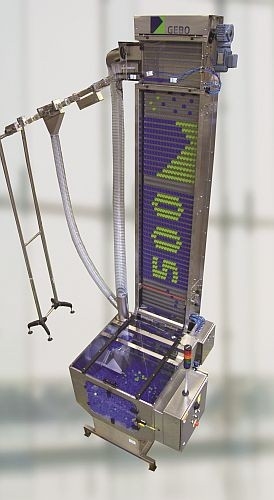
Aidlin cap feeders, at the heart of Gebo’s historic know-how
The first Aidlin cap feeder appeared in Sarasota, Florida, in 1988. Integrated into packaging lines to feed capping machines, the cap feeder stocks, lifts and orientates caps. The machine takes the caps stored in bulk in a hopper at ground level, lifts them via a belt equipped with cleats, and orientates them according to a simple, efficient gravitational principle. Any improperly positioned cap falls back into the hopper, whilst only properly oriented ones continue their journey towards the capping machine.
On a packaging line, the capping / filling machine is very often the critical machine. Supplying the machine demands a very high level of performance, whatever the type of cap, whether it be sports, screw cap or beer crown. With efficiency over 99.5% at low, medium and high throughput, the Aidlin cap feeder perfectly secures supply to the capping / filling machine for optimum line efficiency.
Another advantage of gravitational orientation technology is hygiene. The Gebo cap feeder orientates the cap outside the filling zone. This prevents dust falling into products, which is inevitable when the positioning is done above the capping / filling machine, as is the case with other technologies (where caps are brought in bulk, which is a source of dust and fine PET particles). As a guarantee of improved hygiene for all products, this feature is key for sterile bottling lines, aseptic packaging, or indeed in the case of beer using flash pasteurization technology before filling.
A solution recognized by all markets
Innovation is a key element in caps. On the one hand, progress with materials and the industrial process tend toward regular lightening of materials. Also, shapes need to take on new uses, and have become more complex, like sports caps, for example. Gebo has always been able to adapt Aidlin cap feeders to accompany these market trends. This capacity for innovation confers upon Aidlin cap feeders unparalleled, durable efficiency in every segment: CSDs, water, fruit juice, beer, body care products and detergents. Plus, of course, the potential to meet challenges. For example, Gebo was the first equipment supplier, and indeed the only one to date, to have the necessary know-how to integrate “Waterfall” technology into their high-throughput beer lines with crown caps.
Loved the world over, 1,600 units of Aidlin solutions have been installed to date. Each major market (Europe, North America and Asia) is served by a dedicated Gebo site, which adapts the machines to local conditions, thus reducing transport costs. The manufacture of Aidlin cap feeders spans the world from Laval (Canada), Beijing (China) to Reichstett (France).
The first cap feeder made at the Reichstett plant came out of the workshop in 2001. Increased manufacturing rhythms and upscaling have benefited from modern production management tools such as Lean Management and systematic Factory Acceptance Tests.
With the desire to constantly innovate to accompany cap innovations, and efficient in every context, the Aidlin range intends to continue its development throughout the world, and singularly in Reichstett. Nicolas Bossert, cap feeder and air conveyor department manager in Europe, is looking to the future with optimism: “The success of Aidlin cap feeders continues year after year, and we have great prospects, both on existing markets for drinks and new markets to explore. We are progressing consistently each year. We already have thirty or so cap feeders on order, and new developments expected for 2014.”