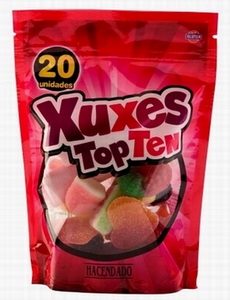
Bulk presentations are usually used for sweets like marshmallows, gummies, and soft candies, representing almost half of the sector sales. In the last few years, the presence of these products in a package suited for sale in gas stations, supermarkets, drugstores, and as a novelty, candies packaged in a stand-up pouch, have been appearing for some time; these packages also feature a zipper reclosing system. This is a user friendly presentation and is attractive when displayed in the point of sale shelves.
For packaging these products in a stand-up pouch with a total guarantee, it is important to have a horizontal pouching system with the ideal dosing system, and the necessary stations to perform the ideal packaging. In some cases, the possibility of treating the product with Nitrogen flushing for Oxygen removal will provide maximum quality.
In these applications we can find products like gum tablets, hard candy, sweets and tablets that are normally dose through a weighing system. Due to the required production speeds, a multi-head weigher is normally chosen; this weigher has different load cells with the objective of achieving the best weight accuracy of the product being packaged.
Once the product is released from the weigher, the intermediate funnels connect the product fall with the expanding funnels that provide the largest bag opening possible and help with the discharge. Generally, to work with fragile products, and to avoid they get damaged, special coating is used to help the product flow towards the bag.
In other cases, when the combination of products is varied, like in goodies with different and unequal quantity of elements, a robotic feeding system has been created capable of counting the exact units which are deposited in a discharge belt, supplying the product combination inside the bag. At the same time, a vision camera makes sure that all the units are grouped inside each bucket and ready for discharge; in case one unit is missing, a reject system evacuates the defective bag before the correct bag discharge.
When the product to be packaged is granulate or powder, auger fillers are utilized with a high degree of finish and polish, which provide an excellent sanitary design and a dosing accuracy with a maximum tolerance deviation of 1%.
Counters or feeders are used to dose some confectionary products.
In some cases, and for large volume products, a station with a pusher can be prepared to ensure the product will not be outside the bag while this is still open, in some other cases, bottom vibrators help the product settle inside the bag.
As a value added, a Nitrogen injection system can be supplied to eliminate the residual oxygen inside the bag in order to extend the life of the product. The nitrogen flush is applied before, during and once the product is in the package. A modified atmosphere is convenient depending on the type of product.
The type of film used for packaging needs to be the right one in terms of width and composition, if not, it can harm the bag making process and affect the product shelf life and package stability. To note that in some cases a third layer barrier can be used to better protect the product. In these cases, we can turn to Aluminum (ALU) and with 9 microns it can be sufficient, with this a three layer film is obtained: PET12/ALU9/PE80, which is quite common and covers a wide range. It is true that in some cases in order to find cheaper film the aluminum has been substituted for a metalized layer based on particulates between the outer non sealing layer (PET) and the internal (PE). When a product contains important sugar content, it is advised to use materials like stainless steel AISI-316, titanium or certain plastic materials which are resistant to these types of products, and that provide the desired results.
When the bag has a certain size and the content will be consumed in several instances, it is recommended to have a reclosable system (Zipper) to preserve the product's properties as much as possible once the bag is open.
On a technical level, the latest technological advances are being used by BOSSAR in the construction of horizontal packaging machines totally built with Servo Control systems, and management programs that allow for more control of the different production stages with independent axes, creating a wide range of possibilities that allow for different film utilization and a personalized and independent variation of the parameters depending on the product conditions. We find cases where we want to increase the sealing time, the pressure or the dosing time, and this variation is achieved in milliseconds bringing more benefits to the package in a simple way and provided better product guarantee.